Endplate assembly was shipped yesterday, 2008-08-26, 13:30.
Arrival at DESY is expected Friday, 2008-08-29.
(This is Federal Express - Express)
update: 2008-08-27: 11:49 CET:
it has left the building in Memphis
update: 2008-08-28: 02:32 CET:
it is in Frankfort.
update: 2008-08-28: 18:02 CET:
it is still in Frankfort.
It seams that it cleared customs, but missed the next flight.
What was sent...
(1) Endplate, serial number 1.
It is the more accurate endplate.
Perimeter dowel holes are with +/-1.1
(The unit is 0.001inch = 25.4microns.)
Backframe mounting holes are within +/-4 (global),
+/-1.2 (local, boundingbox coordinates).
Most are within the goal: +/-0.5 (local).
All surfaces that had "too much material" have been fixed.
(1) Field cage termination assembly.
Wires are mounted - #24 stranded Teflon insulator.
(1) Backframe - "GEM No Gate".
This backframe is to be sent to Bonn at some point.
It is provided as an example,
fully mounted,
dowel pins in-place,
o-ring mounted and compressed.
When you remove/reinstall this Backframe, put the 2 undersize dowels (marked with a facet) back where you found them.
When compressing/decompressing the o-ring, turn the screw about 1/8 turn per sequence. Total compression is 3/4 turn.
(7) Mounting brackets.
The "keeper" screws are in-place
(2 screws, one on each side).
The release ("pusher") screws are in-place
(four screws in the corners, with
rubber sleeves to prevent them from coming out during transit.)
These have rounded tips to prevent scuffing.
(1) Outer (field cage) o-ring.
Getting it out of the box...
Take out all the screws on the top panel.
Lift off the top panel.
Do not drop a corner into the box!
Take out the sheet of cardboard (not shown).
Bend back the retainers that are on the bolt heads.
Remove the (8) bolts, 9/16 wrench (14mm should work).
Lift at the outer rim only.
Do NOT lift using the thin frame sections.
(Do not yank on the mullions.)
Do NOT support on/by the Field Cage Termination plates.
Things about which I am NOT happy...
This is the endplate with the repaired "fun hole", but it should be OK. Forget it.
The surface finish in the light openings is not to-spec.
The finish in the laser opening is worse than that in the opening for the Victoria Light Insert.
We must test this, somehow.
Maybe the surface must be polished.
Maybe the depth of the o-ring grove of the laser access cover, 6080-128, should be decreased about 0.002 inch.
The Field Cage Termination Stand-offs are junk.
The stand-offs cracked when cleaned in ethyl alchohol; they were stessed during machining.
The surface was attacked by ethyl alchohol.
This should not happen with acrylic.
Maybe this is not genuine Rohm and Haas Plexiglass.
I have wrapped the stand-offs in Kapton tape to be able to ship the endplates with the FCT attached.
For the Micromegas, the backframe extends beyond the back surface of the FCY.
We can use metal stand-offs.
I will obtain new stand-offs in aluminum.
We wil have to decide on a stand-off material for the GEM.
In 2 cases, a FCT stand-off overlaps a FCT-HV feedthrough counterbore.
In 1 case, the stand-off o-ring "falls into" the counterbore.
I don't know how this happened. The HV feed-through could have been centered beteen the stand-offs.
The couterbore could have been smaller.
I guess it is a good thing that the stand-offs must be remade.
I will move the o-ring to smaller radius.
Other items that are needed, but missing...
Victoria Light Insert opening blank-off, 6080-127.
Have quote, will order, today - 1 week.
Dowel pins (3mm) for locating MountingBracket-to-Endplate and Backframe-to-MountingBracket.
I provided 8 of these pins with the Endplate shipment.
These are not production.
The full installation required 56 per endplate.
The original Backframes (2008-02-28) have 3.2mm oversize dowel holes.
Some of the new Backframes will have 3.2mm dowel holes.
Undersize pins are required to accomodate small mis-alignments of the holes.
I have ordered a complete set of dowel pins: 3mm-3mm, 3mm-3.2mm, in silicon-bronze.
See 6080-140 and 6080-141 on the drawing page.
(We do not need 3.2mm-3.2mm; the 3.2mm holes will only be in the Backframes.)
The set includes 0.0008inch (20micron) and 0.0016inch (40micron) undersizes for ends which
insert into the Endplate and Backframes.
So, there are 6 different dowel pin sizes.
The end which is inserted into the MountingBracket will be "standard"
Endplates
2008-07-16:
...Corrections defined, endplates back were at vendor
2008-07-30:
...Endplates modifications not complete in 2 weeks; paperwork messed up
2008-08-07:
...Endplates modifications complete
2008-08-13:
...Endplates have been measured with the Cornell CMM.
.. I must review these measurements.
2008-08-18:
...Endplates pass
BackFrames
2008-08-04:
(after making re-measurements to address inconsistancies within the caliper measurements)
... 10 of the 28 Backframes inspected in CMM.
... All inspected by dpp with a caliper.
... Many parts require extra machining of outer-radius surface and repositioning of the holes.
... 5 (out of 6) of the "Micromegas" parts are good.
... The "3GEMNoGate" part is good.
... 2 (of 21) 3GEMG parts are good. I will send them to Bonn.
2008-08-06:
... I had a meeting with the vendor to discuss corrections to the parts.
... All parts measured with CMM. All measurements agree with caliper measurements to 25 microns.
2008-08-13: what I said
... "The parts found "good" with the caliper, 2008-07-30, are still good. I will send them."
2008-08-19:
... Start looking at the "Inside-the-chamber" measurements.
... In many instances, the 2mm hole location is out-of-tolerance.
... It is difficult to correlate the "inside" with the "outside" measurements.
... This is supposed to be done with the Jig 6080-123 (the plate I sent to each of the module producers.)
2008-08-25
...I think I understand the measurements. This can move ahead now that the Endplate assembly is "out the door".
Mounting Brackets
2008-07-16:
...Mounting Brackets complete, delevered to Cornell shop for inspection.
2008-08-13:
... 14 (of 16) Mounting brackets pass inspection. They will be sent with
the endplates..
2008-08-13 production
Endplates
2008-07-16:
...Corrections defined, endplates back were at vendor
2008-07-30:
...Endplates modifications not complete in 2 weeks; paperwork messed up
2008-08-07:
...Endplates modifications complete
2008-08-13: today
...Endplates have been measured with the Cornell CMM.
.. I must review these measurements.
BackFrames
2008-08-04:
(after making re-measurements to address inconsistancies within the caliper measurements)
... 10 of the 28 Backframes inspected in CMM.
... All inspected by dpp with a caliper.
... Many parts require extra machining of outer-radius surface and repositioning of the holes.
... 5 (out of 6) of the "Micromegas" parts are good.
... The "3GEMNoGate" part is good.
... 2 (of 21) 3GEMG parts are good. I will send them to Bonn.
2008-08-06:
...I had a meeting with the vendor to discuss corrections to the parts.
...All parts measured with CMM. All measurements agree with caliper measurements to 25 microns.
2008-08-13:today
...The parts found "good" with the caliper, 2008-07-30, are still good. I will send them.
Mounting Brackets
2008-07-16:
...Mounting Brackets complete, delevered to Cornell shop for inspection.
2008-08-13: today
... 14 (of 16) Mounting brackets pass inspection. They will be sent with
the endplates..
2008-07-30 production
Endplates
2008-06-09: order date +7 weeks:
...Endplates complete, delivered to Cornell shop .(See figure below.)
2008-06-30:
...CMM inspection of endplates completed in Cornell shop. That took 21 days. (See figure below.)
2008-07-10:
Inspection reviewed, requires modification to bring into specification.
.......It is possible there would be interference with BackFrames, if BackFrames are oversize.
2008-07-16:
...Corrections defined, endplates back at vendor, should require 3-5 days.
2008-07-30: today
...Endplates modifications not complete in 2 weeks; paperwork messed up
BackFrames
2008-06-26: order date +9 weeks, 3 days:
...Backframes complete, in Cornell shop.
2008-07-15:
...CMM inspection of Backframes not started; operator was on vacation. But, there is a defined program.
2008-07-30: today
...10 of the 28 Backframes inspected in CMM.
All inspected by dpp with a cailper.
Measurements agree when there are CMM measurements.
... Many parts require extra machining of outer-radius surface and repositioning of the holes.
... 5 (out of 6) of the "Micromegas" parts are good.
... The "3GEMNoGate" part is good.
... 1 (of 21) 3GEMG parts are good. I will send it to Bonn.
Mounting Brackets
2008-07-16:
...Mounting Brackets complete, delevered to Cornell shop for inspection.
.... I will do the inspection with hand tools to speed this up.
2008-07-16 production
Endplates
2008-06-09: order date +7 weeks:
...Endplates complete, delivered to Cornell shop .(See figure below.)
2008-06-30:
...CMM inspection of endplates completed in Cornell shop. That took 21 days. (See figure below.)
2008-07-10:
Inspection reviewed, requires modification to bring into specification.
.......It is possible there would be interference with BackFrames, if BackFrames are oversize.
2008-07-16: today
...Corrections defined, endplates back at vendor, will require 3-5 days.
BackFrames
2008-06-26: order date +9 weeks, 3 days:
...Backframes complete, in Cornell shop.
2008-07-15:
...CMM inspection of Backframes not started; operator was on vacation. But, there is a defined program.
Mounting Brackets
2008-07-16: today
...Mounting Brackets complete, to be delevered to Cornell shop for inspection.
.... Maybe I will do the inspection with hand tools to speed this up.
2008-07-02 production
2008-06-09: order date +7 weeks:
...Endplates complete,in Cornell shop .(See figure below.)
2008-06-26: order date +9 weeks, 3 days:
...Backframes complete, in Cornell shop.
2008-06-27:
...Mounting Brackets delivered with +250 micron cut.
2008-06-30:
...CMM inspection of endplates completed in Cornell shop. That took 21 days. (See figure below.)
...But, dpp must review the inspection.
2008-07-01:
...Mounting Brackets returned to vendor for final cut.
...CMM inspection of Backframes not started, but, there is a defined program.
2008-06-18 production
2008-06-09: order date +7 weeks:
Endplates complete,in Cornell shop waiting for inspection. (See figure below.)
2008-06-12: order date +7 weeks, 3 days:
Backframes delivered with +250 micron cut.
2008-06-13: order date +7 weeks, 4 days:
Discovered problems with tooling during inspection of Backframes with +250 micron cut.
Backframes returned to vendor for final cut.
Mounting Brackets delivered with +750 micron cut.
2008-06-16:
Inspection defined and started in Cornell shop. (See figure below.)
2008-06-17:
Mounting Brackets returned to vendor for second cut.
Backframe final cut, in progress; discussed revised tooling. (See figure below.)
2008-06-04 production
2008-05-21: order date +4 weeks, 2 days:
Endplates delivered with +250 micron cut.
Endplates are cold-shocked in liquid nitrogen.
2008-05-22: order date +4 weeks, 3 days:
Endplates are returned to vendor for final cut.
2008-05-23:
Field Cage Termination delivered.
2008-05-30: order date +5 weeks, 4 days:
Backframes delivered with +750 micron cut.
Backframes are cold-shocked in liquid nitrogen.
2008-06-02: order date +6 weeks:
Backframes are returned to vendor for second cut.
2008-06-09: order date +7 weeks:
Endplates complete,in Cornell shop waiting for inspection
2008-06-12: order date +7 weeks, 3 days:
(expected) Backframes delivered with +250 micron cut
2008-05-20 production
2008-05-16: order date +3 weeks, 4 days:
Endplates delivered with +750 micron cut.
Endplates are cold-shocked in liquid nitrogen.
2008-05-19: order date +4 weeks:
Endplates are returned to vendor for second cut.
2008-05-21: order date +4 weeks, 2 days:
10:00 (NewYork): Endplates ready at vendor with +250 micron cut.
2008-05-12 production
2008-05-12: order date +3 weeks:
tooling jig is complete; endplate is mounted on the milling machine.
The brass nut things are used to stabilize the mullions.
2008-05-07 production
Orders were placed 2008-04-08. They say delivery is in 6 weeks.
But, it was not until 2008-04-21 that the order passed through Cornell purchasing.
2008-05-05: order date +2 weeks:
water-jet cutting for Endplates was completed.
This week: will go on milling machine for +0.030inch (75 micron) cut.
2008-02-25 Module Back-Frames
6 Module Back Frames have been produced: (2) 3GEMG, (2) Micromegas, (2) pixelGEM.
The measurement jigs have been remade.
Holes are within 0.018mm (0.0007 inch).
Re-machining is complete.
Measurements are complete.
Measurements have been reviewed.
The holes have been moved to the correct locations (and enlarged from 3.000mm (0.1181 inch) to 3.200mm (0.1260 inch).
Holes locations are within 0.025mm (0.0010 inch) of design.
Holes in jigs are 0.1250 inch; holes in Back-Frames are 0.1260 inch.
Back-Frames fit onto jigs with 4 dowels, size 0.125 inch.
Back-Frames and measurement jigs will be shipped Wednesday.
2008-02-12 Module Back-Frames
6 Module Back Frames have been produced: (2) 3GEMG, (2) Micromegas, (2) pixelGEM.
(reminder from 2008-01-16)
The holes for locating the PCB (pad board) were not installed
There is a problem with the dowel holes for locating the backframe to the mounting bracket (6080-110).
....... (Certification measurements shown on pages 8-12 of the drawing 6080-104,
go to the page of current drawings
)
And, the measurement jigs are out of tolerance.
(Measurement jig is shown in drawing 6080-123, and 6080-104-sheet 12,
go to the page of current drawings
)
Certification measurements are made relative to the blue axis, centered on the lower-right hole and with the lower-left hole defined as y=0.
The spacing of holes, in the "x" direction,
over the width of the part
(as shown by the pink dimension indicators in the figure on the right)
are out-of tolerance.
The "x" measurement, across the part, is small by 0.10mm (0.004 inch). This is consistant for all 6 parts; the error is 0.004 +/- <0.001 inch.
All other dimensions are within 0.025mm (0.001 inch).
As of Tuesday 2008-02-12...
The measurement jigs have been remade. Holes are within 0.018mm (0.0007 inch).
Re-machining is complete.
The holes have been moved to the correct locations (and enlarged from 3.000mm (0.1181 inch) to 3.200mm (0.1260 inch).
Measurements on the backframes, and the backframes mounting on the measurement jigs, are complete.
I have reviewed the measurements on one BackFrame; it is good.
I will review the measurements on the other 5 BackFrames.
....... (Again, certification measurements shown on pages 8-12 of the drawing 6080-104,
go to the page of current drawings
)
2008-01-29 Module Back-Frames
6 Module Back Frames have been produced: (2) 3GEMG, (2) Micromegas, (2) pixelGEM.
(reminder from 2008-01-16)
The holes for locating the PCB (pad board) were not installed
There is a problem with the dowel holes for locating the backframe to the mounting bracket (6080-110).
....... (Certification measurements shown on pages 8-12 of the drawing 6080-104,
go to the page of current drawings
)
And, the measurement jigs are out of tolerance.
(Measurement jig is shown in drawing 6080-123, and 6080-104-sheet 12,
go to the page of current drawings
)
Certification measurements are made relative to the blue axis, centered on the lower-right hole and with the lower-left hole defined as y=0.
The spacing of holes, in the "x" direction,
over the width of the part
(as shown by the pink dimension indicators in the figure on the right)
are out-of tolerance.
The "x" measurement, across the part, is small by 0.10mm (0.004 inch). This is consistant for all 6 parts; the error is 0.004 +/- <0.001 inch.
All other dimensions are within 0.025mm (0.001 inch).
As of Monday 2008-01-28, the holes are being moved to the correct locations (and enlarged from 3.000mm (0.1181 inch) to 3.200mm (0.1260 inch).
The measurement jigs have been remade. Holes are within 0.018mm (0.0007 inch).
Measurements on the backframes, and the backframes mounting on the measurement jigs, will be made soon.
....... (Again, certification measurements shown on pages 8-12 of the drawing 6080-104,
go to the page of current drawings
)
2008-01-11 Module Back-Frames
6 Module Back Frames have been produced: (2) 3GEMG, (2) Micromegas, (2) pixelGEM.
The holes for locating the PCB (pad board) were not installed
There is a problem with the dowel holes for locating the backframe to the mounting bracket (6080-110).
....... (Certification measurements shown on pages 8-12 of the drawing 6080-104,
go to the page of current drawings
)
And, the measurement jigs are out of tolerance.
(Measurement jig is shown in drawing 6080-123, and 6080-104-sheet 12,
go to the page of current drawings
)
Certification measurements are made relative to the blue axis, centered on the lower-right hole and with the lower-left hole defined as y=0.
The spacing of holes, in the "x" direction,
over the width of the part
(as shown by the pink dimension indicators in the figure on the right)
are out-of tolerance.
The "x" measurement, across the part, is small by 0.10mm (0.004 inch). This is consistant for all 6 parts; the error is 0.004 +/- <0.001 inch.
All other dimensions are within 0.025mm (0.001 inch).
The holes will be moved to the correct locations (and enlarged from 3.000mm (0.1181 inch) to 3.200mm (0.1260 inch)
The measurement jigs are being remade.
And, the wolves are at the door; there are other demands on the machine shop.
2007-12-04 Module Back-Frames
Module Back-Frames are in production.
Machining step 2 (+0.25mm) and second cold treatment are completed.
The pictures show the cold treatment.
Third maching step (final) starts 2007-12-05, complete 2007-12-07.
Certification measurements during week of 2007-12-10
Measurements are shown on pages 8 and 9 of the Backframe drawing, 6080-104.
.......
go to the page of current drawings
Note that there are 6 parts.
These are 2 for 3GEMG, 2 for Micromegas, 2 for pixelGEM.
Shipment ~2007-12-18. You will receive (2) Backframes, (1) Jig (6080-123), certification measurements.
2007-11-20 Module Back-Frames
Module Back-Frames are in production - late.
There were delays due to misunderstandings while I was away at Fermilab, and
I got bumped by ERL, again.
Note that there are 6 parts: 2 cut flat, 3 with inside cut, 1 on the machine.
These are 2 for 3GEMG, 2 for Micromegas, 2 for pixelGEM.
The other thing on the cart is a jig for holding the parts while cutting the outside.
Thursday and Friday are off for Thanksgiving. I am fortunate that the machininst on this job is not a deer hunter.
PRESENTATIONS
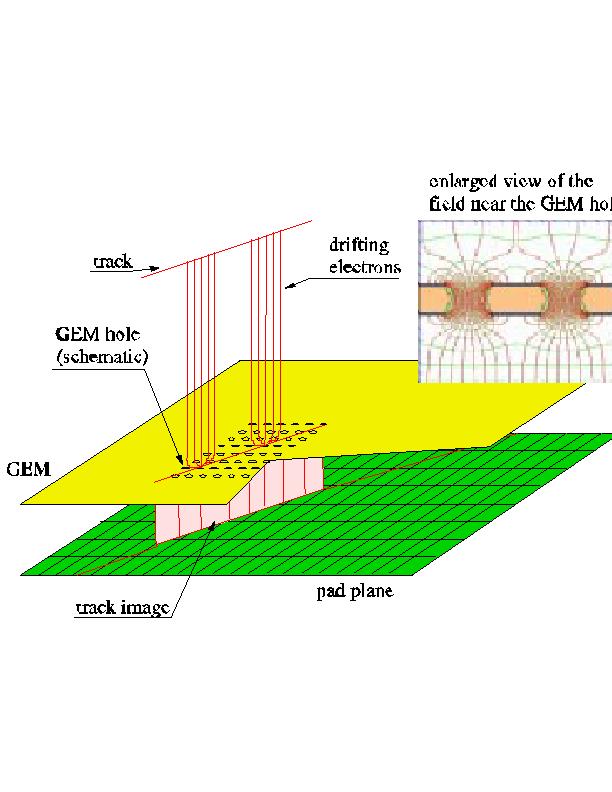
(purdue)